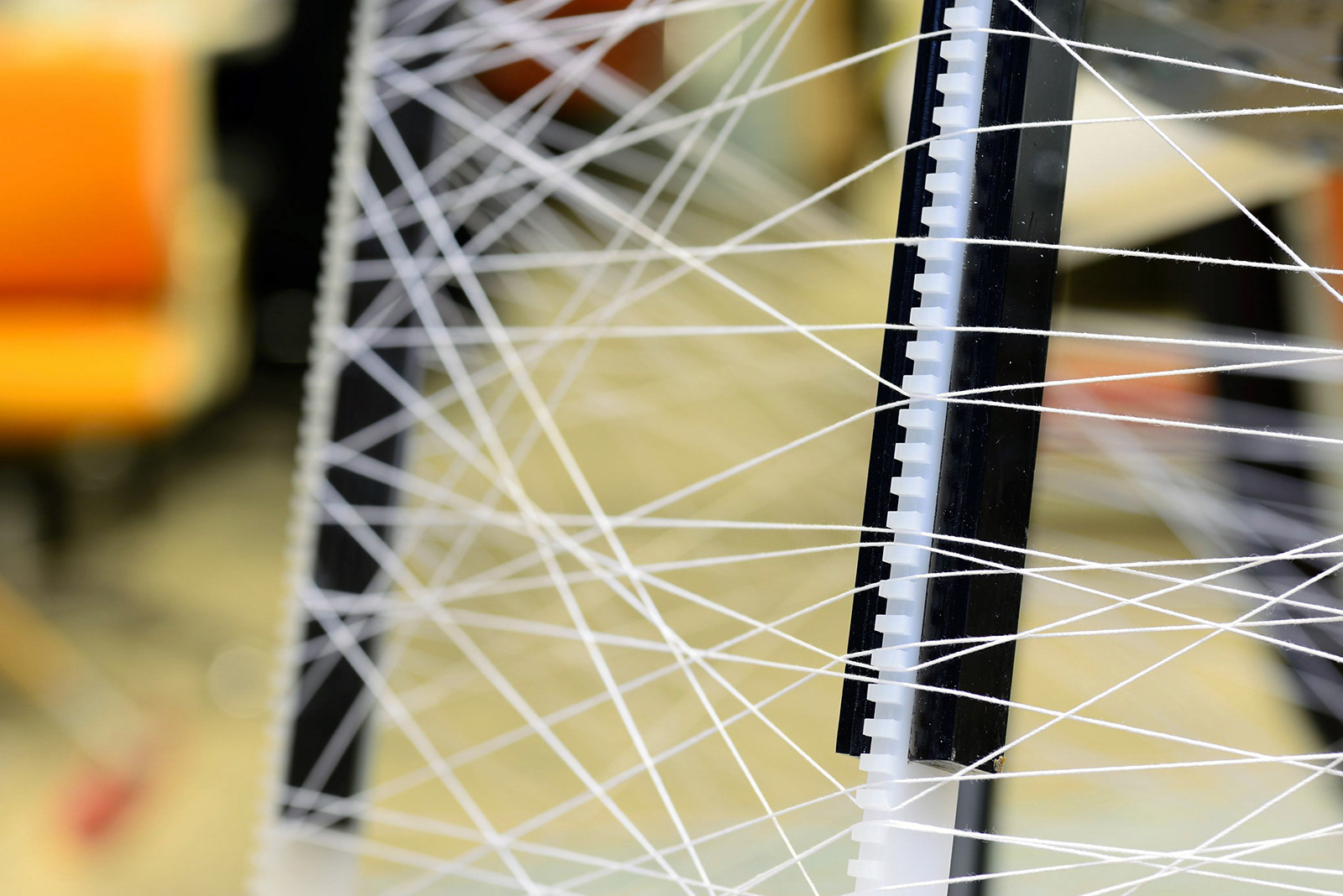
roboWINDER v.6.0 CFRP winding prototype
PRINCIPAL INVESTIGATORS: Andrew John Wit
STUDENT RESEARCHERS: Daniel Eisinger + Steven Putt
PROJECT STATUS: Complete
PUBLICATIONS:
1. 2015 eCAADe Conference Proceedings. “The One Day House. Intelligent systems for adaptive buildings.”
2. Robot 2015 Conference Proceedings. Springer Book Chapter. “Human Interaction-Oriented Robotic Form Generation”
2. Robot 2015 Conference Proceedings. Springer Book Chapter. “Human Interaction-Oriented Robotic Form Generation”
DESCRIPTION: As development of the “One Day House” continues, a series of robotic end effector studies were created and tested with the goal of redefining the methods and materials necessary for small-scale building construction. These studies are on going and have taken many forms.
Rather than looking at a large-scale continuous structural wrapper, ROBO-WINDER investigates a system of smaller unique modular units. With the ability to be designed, fabricated and assembled on-site with minimal effort and material waste, ROBO-WINDER aims to physically and visually re-imagine what housing should look like in the near future. Through the utilization of this system, the buildings form now has the ability to remain flexible, as we are no longer constrained by the form and cross sections of standardized materials such as wood, steel and glass. Complex surfaces can now be optimized and broken down into easy fabricated and workable modules.
Initial Prototyping:
Initial prototyping was accomplished through a simple modular system allowing for the users to create a large variety of symmetrical or asymmetrical structural modules for the construction of the “One Day House”. Early prototypes, focused on the panelization of the skin modules into 3D forms in relationship to the carbon fiber modules. As these tests focused more on winding methodologies and end effectors, structural rigidity and module connection points came in later studies.
Each prototype was designed with ease of assembly and robotic actuating in mind. Prototypes were created to be simply laser-cut or water-jet cut, and bolted together within minutes. Each prototype also allowed for a large amount of programmed variation. Users were able to adjust the length of each arm, as well as their angle of attack through a series of simply defined sliders. This flexibility allowed for the creation of modules with huge levels of variation.
Further Development:
Initial testing allowed for a robust understanding of robotic winding and complex form generation through robotic end effectors and computational design. These tests though lacked the necessary structure to create larger scale projects with longer life-spans.
The next phase of development questions the formal logic of the module while creating a more robust three-dimensional carbon fiber network for structural applications. Through material explorations and structural tests, we hope that future versions of ROBO-WINDER will allow for a novel system for the creation of rapidly produced housing.
Initial Prototyping:
Initial prototyping was accomplished through a simple modular system allowing for the users to create a large variety of symmetrical or asymmetrical structural modules for the construction of the “One Day House”. Early prototypes, focused on the panelization of the skin modules into 3D forms in relationship to the carbon fiber modules. As these tests focused more on winding methodologies and end effectors, structural rigidity and module connection points came in later studies.
Each prototype was designed with ease of assembly and robotic actuating in mind. Prototypes were created to be simply laser-cut or water-jet cut, and bolted together within minutes. Each prototype also allowed for a large amount of programmed variation. Users were able to adjust the length of each arm, as well as their angle of attack through a series of simply defined sliders. This flexibility allowed for the creation of modules with huge levels of variation.
Further Development:
Initial testing allowed for a robust understanding of robotic winding and complex form generation through robotic end effectors and computational design. These tests though lacked the necessary structure to create larger scale projects with longer life-spans.
The next phase of development questions the formal logic of the module while creating a more robust three-dimensional carbon fiber network for structural applications. Through material explorations and structural tests, we hope that future versions of ROBO-WINDER will allow for a novel system for the creation of rapidly produced housing.
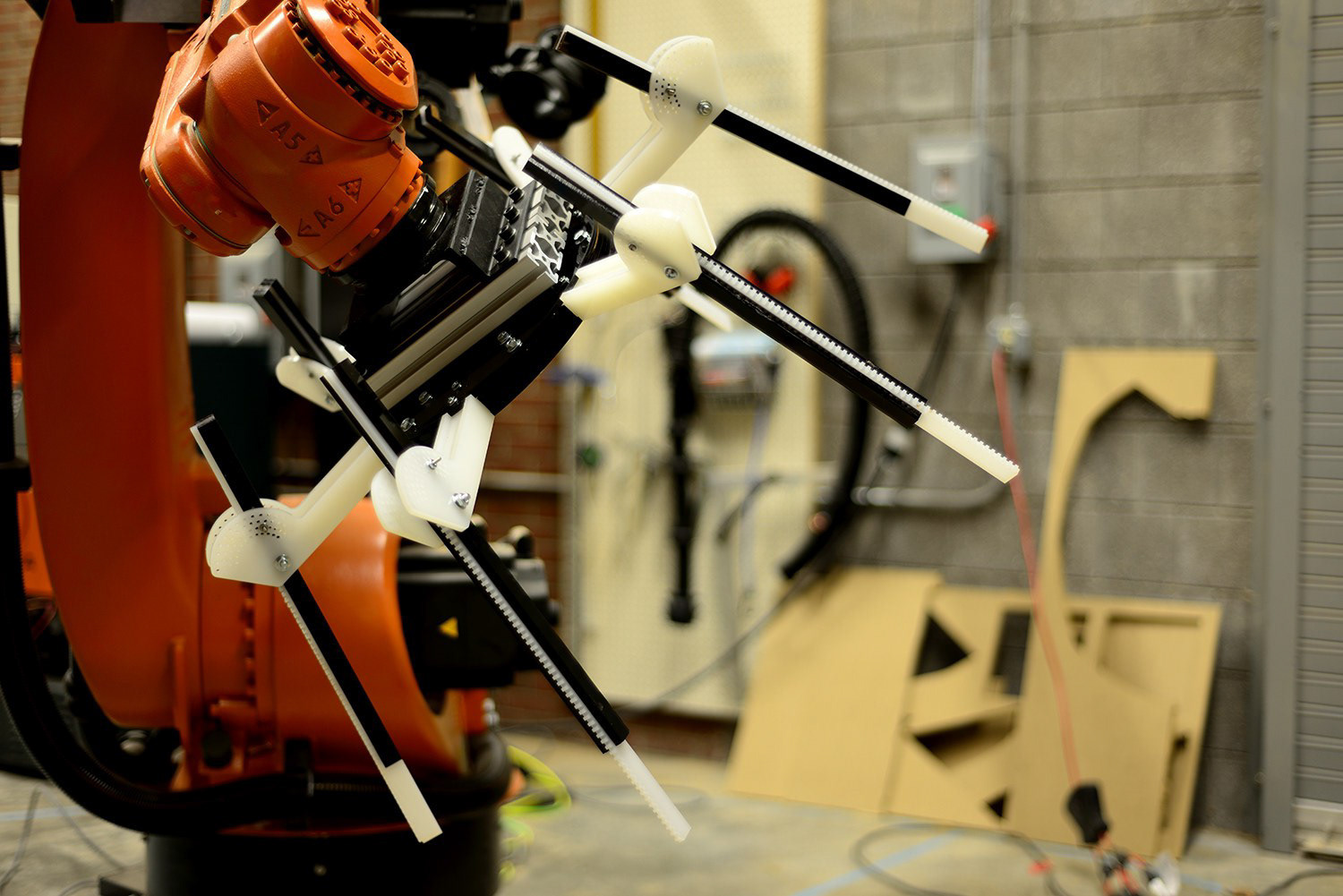
roboWINDER v.6.0 CFRP winding prototype
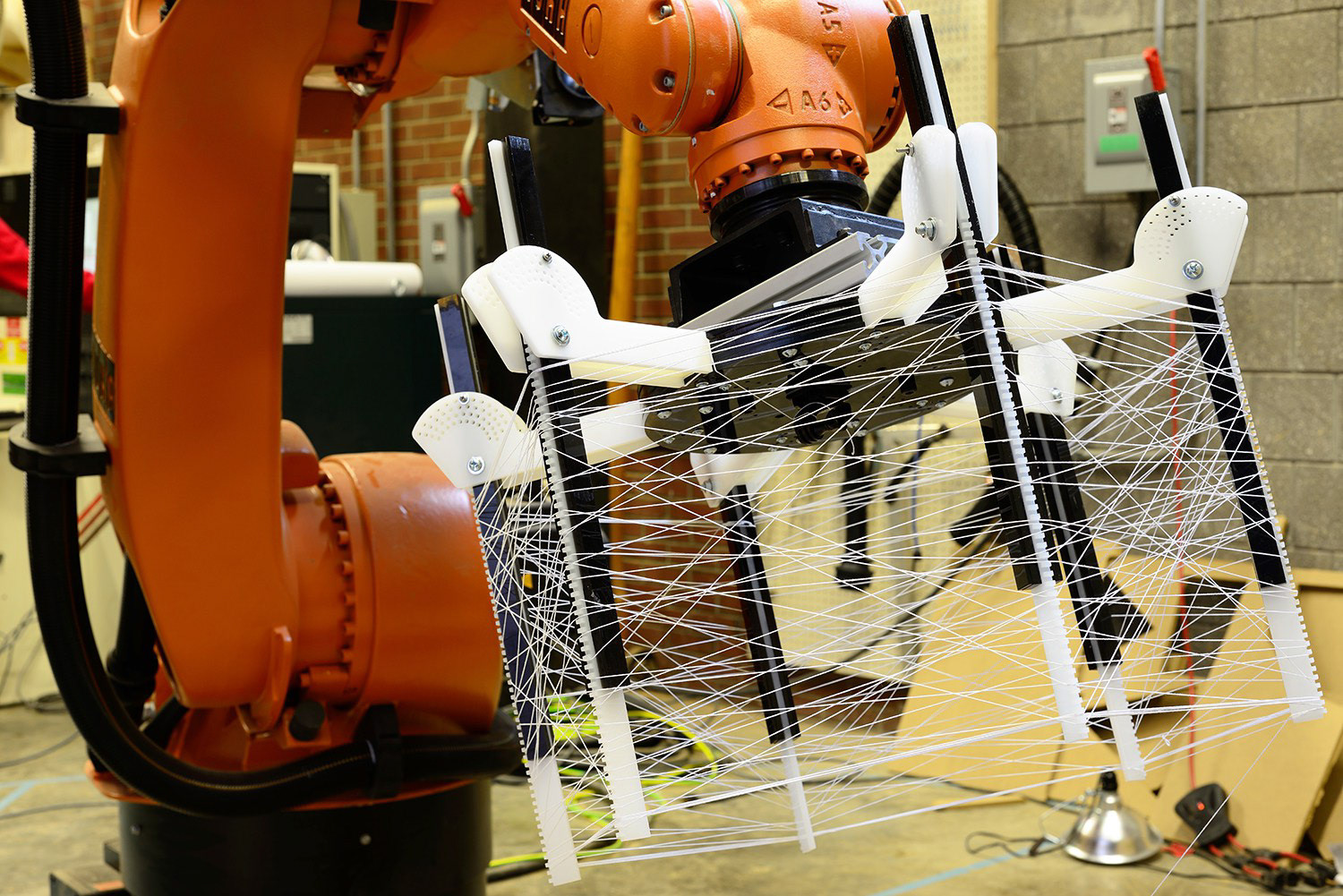
roboWINDER v.6.0 CFRP winding prototype
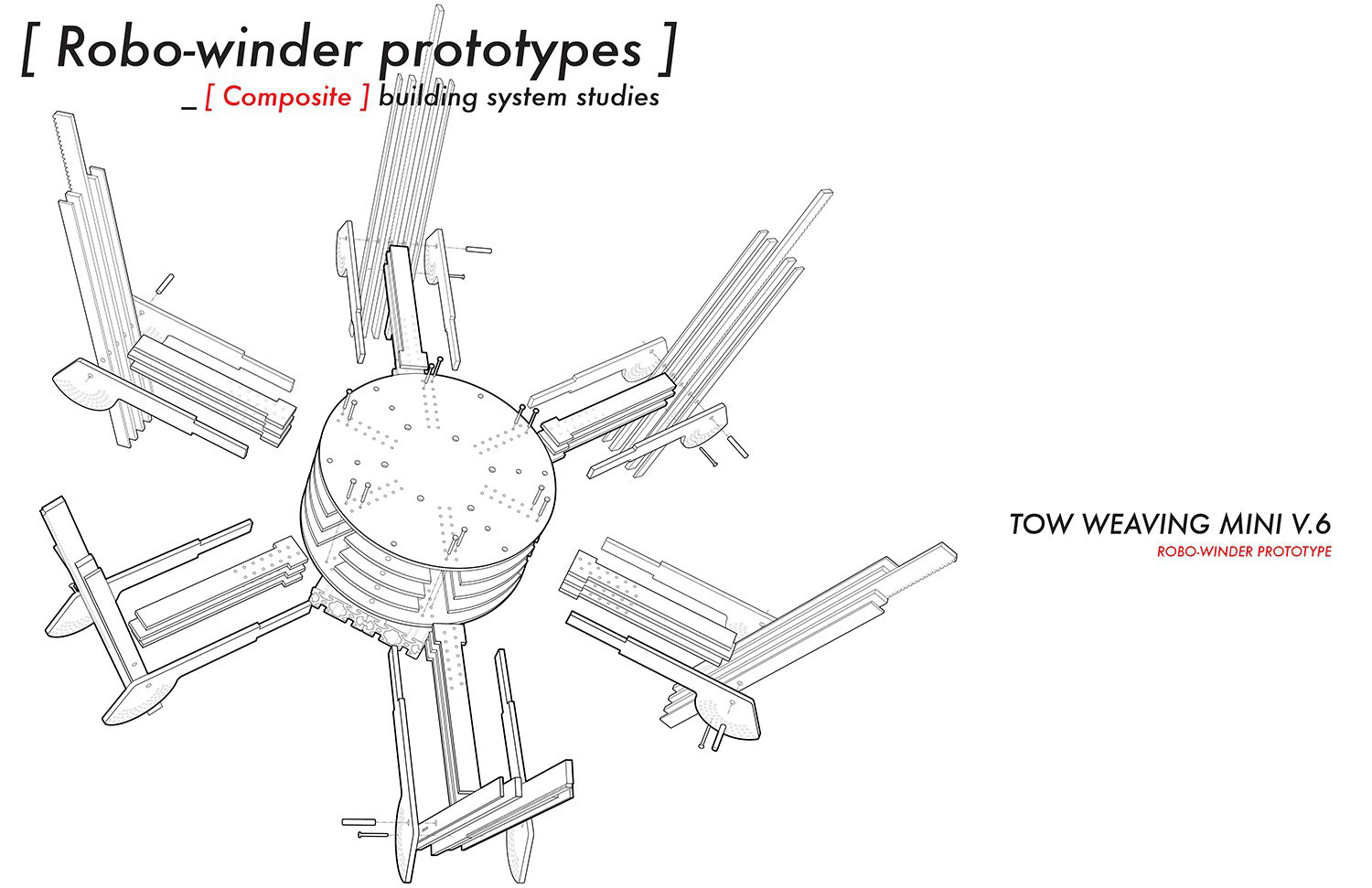
roboWINDER v.6.0 CFRP winding prototype
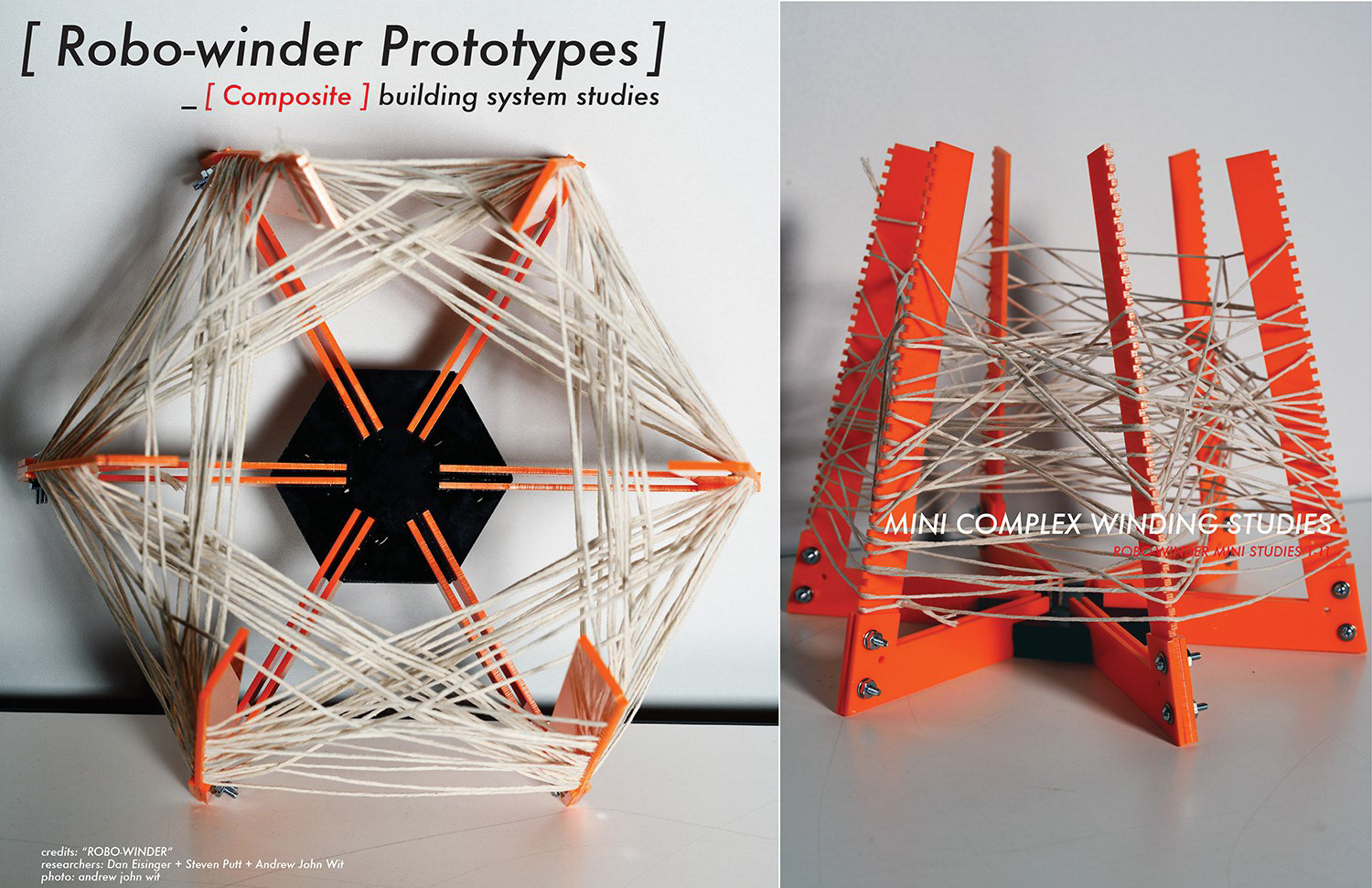
roboWINDER v.7.0 CFRP winding prototype
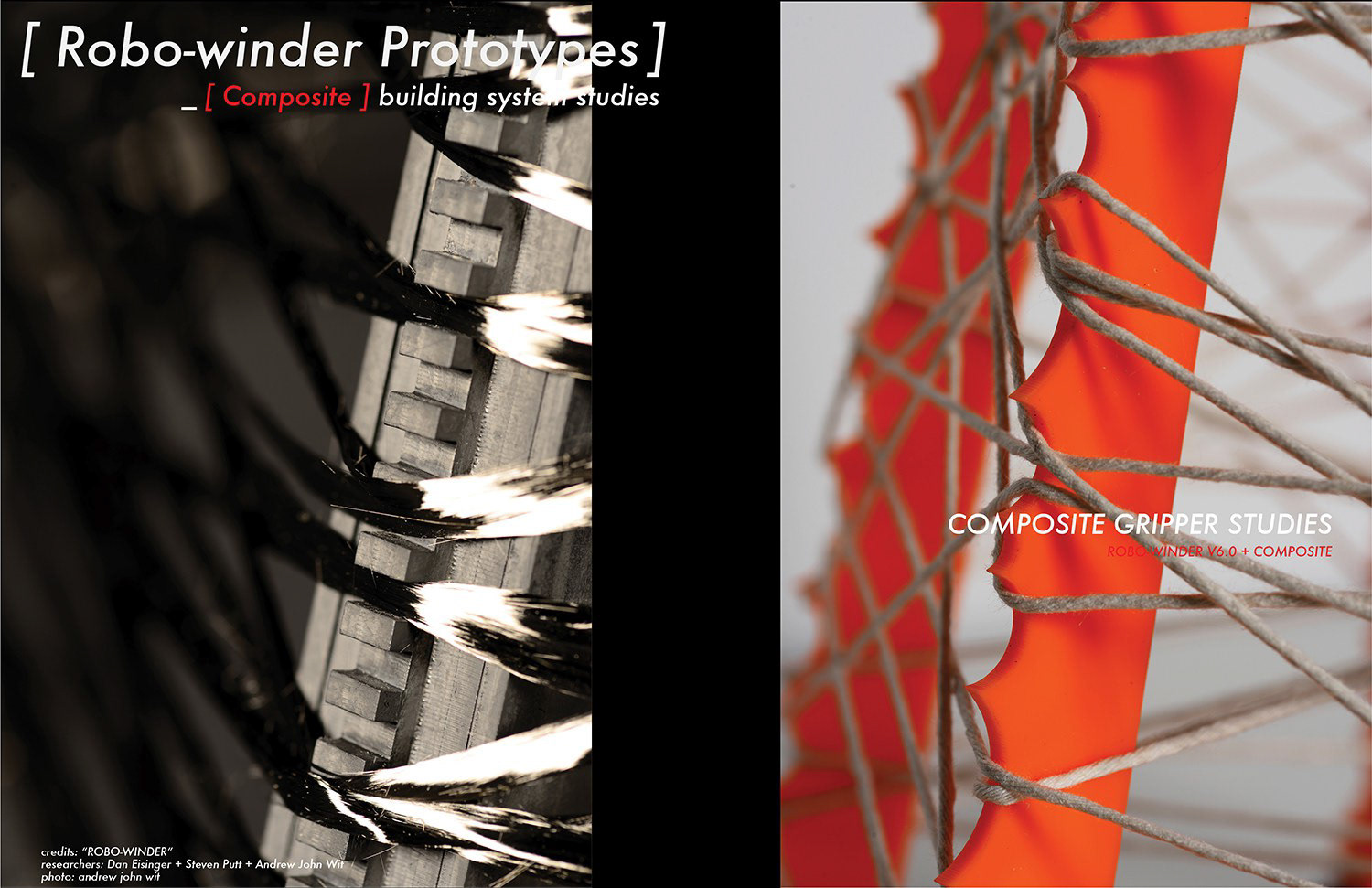
roboWINDER v.6.0 + v.7.0 CFRP gripper prototypes
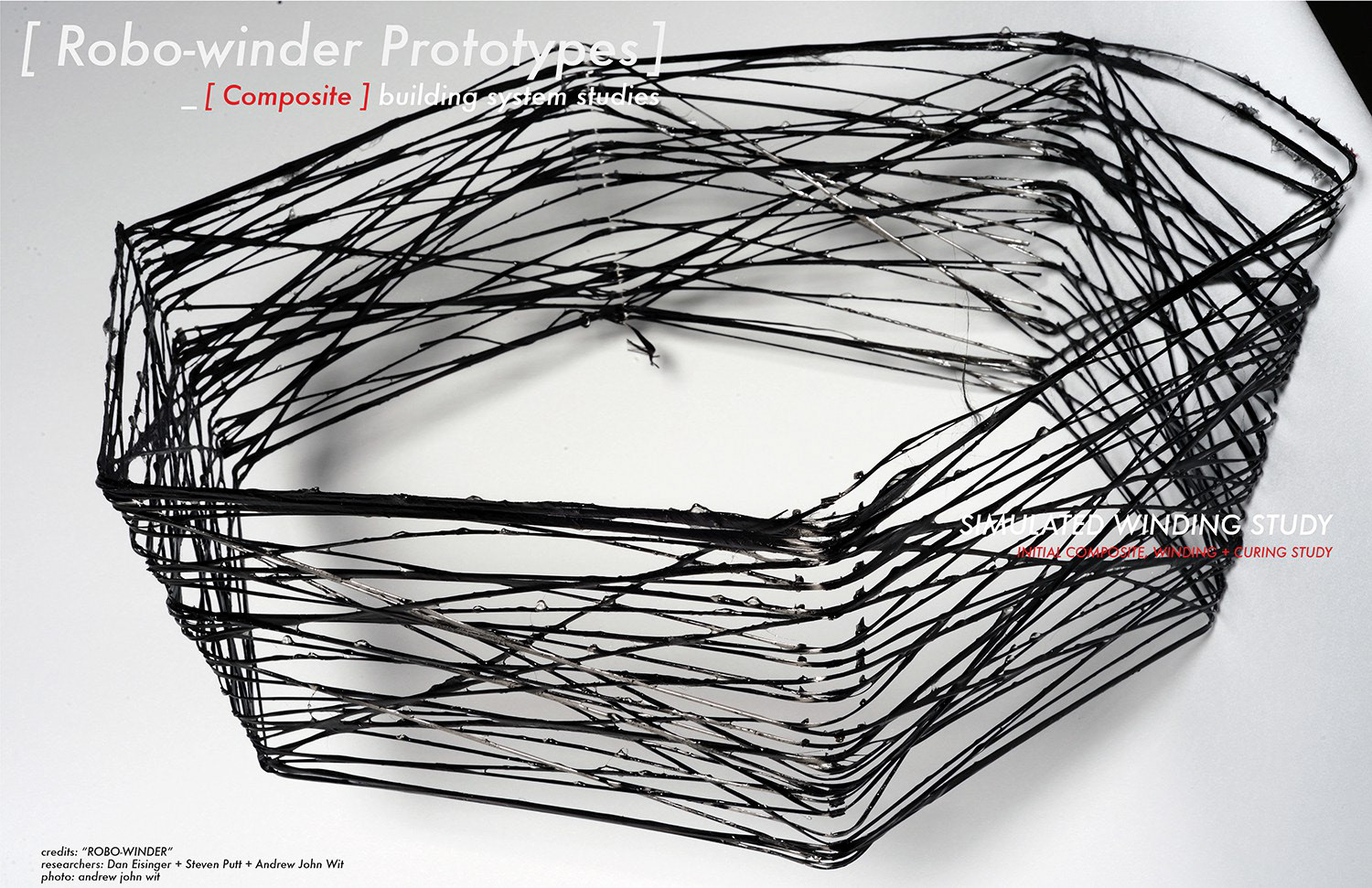
roboWINDER v.6.0 Test Wind
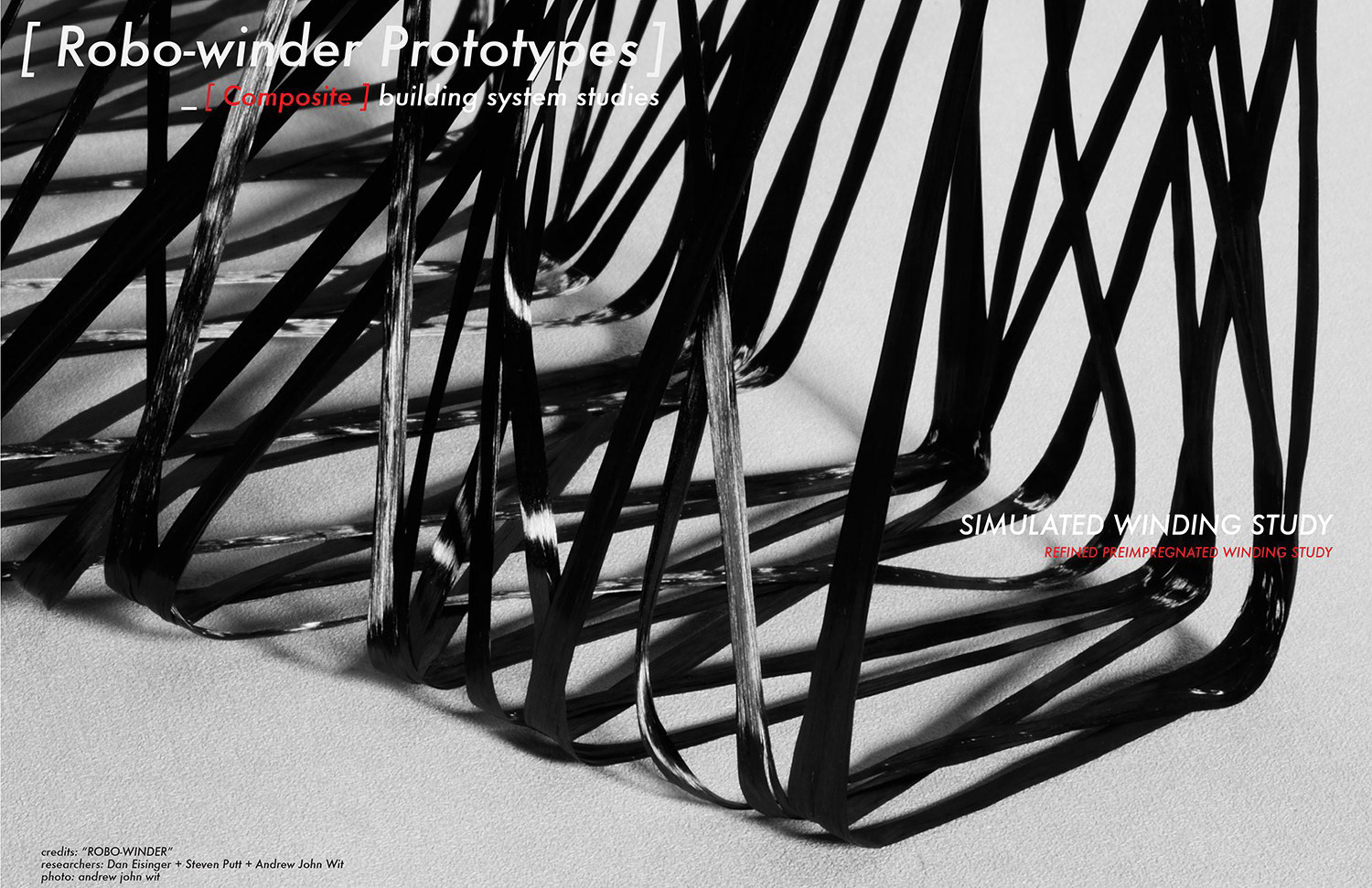
roboWINDER v.8.0 CFRP winding prototype